بازرسی بر مبنای ریسک - Risk Based Inspection (RBI)
(RBI) چیست؟
RBI ابزار مدیریتی است که برای تشخیص و اولویت بندی ریسک های مربوط به تجهیزات تحت فشار، دما بالا و بحرانی و ارائه برنامه بازرسی براساس ریسک های محاسبه شده بکار می رود.
بطور خلاصه در روش RBI میزان احتمال و نتیجه از کار افتادگی تجهیزات محاسبه شده و از ضرب این دو فاکتور (یعنی احتمال و نتیجه) میزان ریسک بدست می آید و براساس اندازه ریسک بدست آمده، برنامه بازرسی برای آنها تعریف می شود.
بازرسی بر مبنای ریسک Risk Based Inspection روش نوینی در بازرسی و تعمیرات پیشگیرانه بوده که با توجه به تأثیرات بسیار مثبت آن، اخیراً به صورت فراگیر در حال اجرا و پیگیری می باشد. کلیه الزامات RBI تحت عنوان API-581 به صنعت معرفی شده و نرم افزارهای مربوطه نیز توسط شرکتهای مختلف خارجی در چارچوب الزامات استقرار سیستم RBI تهیه شده اند.
این نرم افزار باعث می شود که بیشتر منابع بازرسی به سمت اجراء با ریسک بیشتر سوق داده شود و بخش کوچکی از این منابع بر روی اجزاء با ریسک کوچکتر متمرکز گردد.
بازرسی بر مبنای ریسک در مفهوم مدیریت یکپارچه به عنوان یک ابزار کلیدی در بهبود ایمنی صنعتی، بازدهی رقابت پذیری بکار می رود. انجمن نفت امریکا API به عنوان معتبرترین مرجع در زمینه ارائه برنامه بازرسی برمبنای ریسک (RBI) در سند API-581 سه روش را ارائه داده است.
۱- روش کیفی ۲- روش کمی ۳- روش نیمه کمی
روش کیفی (Qualitative Approach): ساده ترین و سریعترین روش می باشد و براساس اطلاعات توصیفی و استفاده از تجربه و کارشناسی مهندسان می باشد و ورودی اطلاعات در این روش غالباً به صورت محدوده هایی از داده به جای اعداد دقیق است.
روش کمی (Quantitative Approach): آنالیز کمی از مدلهای منطقی برای ترسیم ترکیب رویدادهای منجر به خرابی/ حوادث می باشد و نتایج حاصله عمدتاً به صورت اعداد ریسک بیان می گردد.
روش نیمه کمی (Semi-Quantitative Approach): این روش ترکیبی از دو روش بالا می باشد و از سرعت روش کیفی و دقت روش کمی استفاده می گردد.
جهت در نظر گرفتن فاکتورهای ریسک تجهیزات، موارد زیر عنوان می گردد:
مثالی از فاکتورهای خوردگی یک لوله یا تجهیز (Damage Factor):
– اگر مکانیزم های تخریب فعالی وجود دارد که می تواند باعث خوردگی و ترک خوردن در فولادهای کرنبی شود. DF1=5
– اگر تجهیز در شرایطی است که در اثر خستگی مکانیکی یا حرارتی بوجود آمده، دچار مشکل می شود. DF2= 4
– اگر حمله هیدروژنی در دمای بالا وجود داشته باشد. DF3=3
– اگر ترک خوردن توأم با خوردگی در فولادهای زنگ نزن آستینتی در فرایند وجود داشته باشد. DF4=3
– اگر خوردگی موضعی باشد. DF5=3
– اگر خوردگی عمومی باشد. DF6=2
– اگر خزش در فرآیندهای دمای بالا از جمله در کوره ها و هیترها باشد. DF7=1
– اگر مواد و تجهیز در اثر فازهای سیگما، کربوریزاسیون و .. اتفاق بیافتد DF8=1
– اگر مکانیزم های تخریب فعال دیگری باشد DF9=1
– اگر مکانیزم های تخریب بالقوه در واحد عملیاتی، ارزیابی نشده و بصورت دوره ایی توسط یک مهندس مواد با تجربه مورد بازنگری قرار نگرفته DF10=10
در اینجا فاکتورهای دیگر را نیز می توان منظور کرد و سپس با محاسبه آنها عدد ریسک را برای سیستم مدیریت بازرسی فنی بدست آورد.
مزایای بازرسی بر مبنای ریسک:
۱- اثربخشی و کارایی بازرسی فنی
۲- شناسایی پتانسیل های خرابی و شکست
۳- شناسایی نقاط ضعف تجهیزات و تلاش بر بهبودی سیستم
۴- کاهش هزینه های بازرسی- تعمیرات- نگهداری
۵- داشتن برنامه مدون بازرسی براساس ماتریس خروجی سیستم
۶- دسترسی سریع به اطلاعات و سوابق تجهیزات جهت برنامه ریزی آتی
۷- شناسایی موانع تولید براساس آنالیز ستاده ها
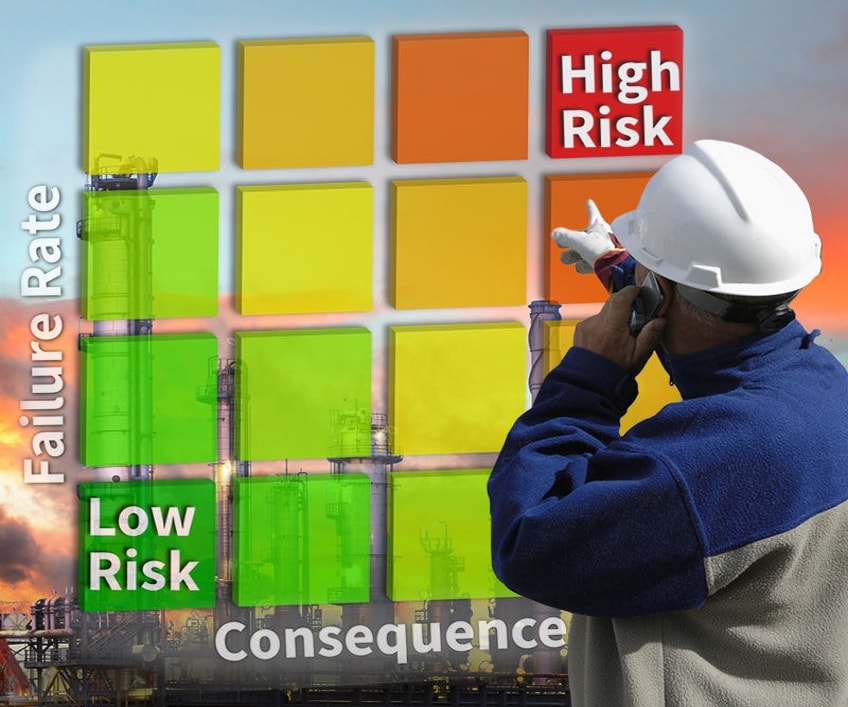